挤压型材时,制品的形状失去对称性,使型材挤压中金属流动不均匀性比圆形端面的制品严重得多,导致挤压型时出现扭曲、弯曲和波浪等缺陷。
这类挤压缺陷的产生主要是模孔实际中的模孔排列、模子工作带设计不当、模子加工精度差、模子的磨损和模孔润滑不均匀等原因造成制品端面上各处金属流动不均匀所致。
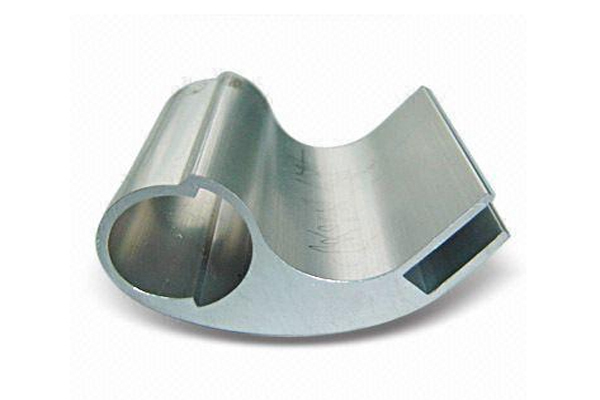
总结发生挤压型材扭转和弯曲的主要原因:
第一,铸棒温度不均衡;
第二,挤压杆、筒、模具三者同心度不好;
第三,模具设计制造误差大,工作带设计不合理;
第四,冷床吹风冷却分布不合理;
第五,无牵引机。
如何防止挤压型材扭转和弯曲呢?下面将详细介绍
首先要从挤压模设计上来考虑,尽量避免型材各部分流出速度不等的现象。方法主要有:模子采用不用工作带长度设计,流动快的部位工作带长一些;设置辅助孔,尽量使模孔截面对称分布。其次,保证模孔加工精度及润滑尽可能一致。还可以在生产中加装导路,使挤压型材出模孔后直接进入导路或牵引装置,趁热强制矫正。一旦挤出成品出现上述缺陷,可以采取拉伸矫直的方法进行挽救。经常检查模孔的磨损情况,及时更换磨损的模具。